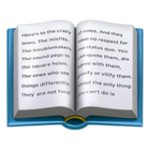
This is four years before I reached that stage and two years before any of my three sisters or sister-in-law hit this developmental milestone. While nine is still considered in the normal developmental range for girls in the United States, it is certainly early compared to the women in my generation.
As HBN’s Chief Research Officer, it is my job to understand the impacts that different chemicals can have on human health and work every day to help people make informed decisions about the products they use. As a mother, it is also my job to keep my kids safe. While my research will not help me answer the question about why my daughter may be going through puberty earlier than I did, I can share what I have learned about chemicals found in building materials and their potential impacts on children’s health in the hope that you can join me in making the best decisions we can for our future generations.
While this article will focus on one environmental factor (exposure to pollutants related to the use of building products), I recognize this is one of many factors that impact children’s health. These include biological factors (e.g. sex, genetics, age), social factors (e.g. income, culture), and environmental factors (e.g. diet, exposure to pollutants).1 With this in mind, this article does not tie specific products or chemicals to specific health outcomes in children. Instead, this article discusses two groups (or classes) of chemicals used in building products that are known to have reproductive toxicity or endocrine disrupting concerns and are found both in household dust and children’s bodies.
Children are not little adults. For example, my five year old likes to sleep in a small cardboard box at night these days with his neck at an angle that would take me weeks to uncrick. They also eat more, inhale more, and drink more than adults per kilogram body weight.2 They also spend more time on the floor (see box story above) and are therefore more likely to ingest or inhale household dust. Their immune and metabolic systems are not fully developed, so their bodies process and eliminate chemicals differently than adults. Lastly, children’s bodies are in a constant state of growth and development, and as such they can be more sensitive to chemicals than adults.3
Let’s explore two groups of chemicals found in building products and in children’s bodies that can impact the endocrine systems.
Bisphenols are a group of chemicals including bisphenol A (BPA) and bisphenol S (BPS). BPA is on the EU Substances of Very High Concern (SVHC) list due to endocrine disrupting properties. Specifically, many bisphenols mimic the hormone estrogen. BPA is considered “Toxic to Reproduction” by the European Chemicals Agency. Bisphenols are found in many different types of products including plastic items, paper receipts, and metal food and beverage can liners. In building products, BPA-related compounds are found in “epoxy” resin products, for example, epoxy flooring adhesive and epoxy fluid-applied flooring.
In last year’s article, “There’s What In My Body?” I shared how I found BPA and BPS in my body through a biomonitoring study by Silent Spring. Compared to other participants in the study, I had lower levels of BPA but higher levels of BPS, a common replacement for BPA. I was surprised and disturbed by the results, and I cannot help but wonder what my daughter’s levels would be today if we tested for bisphenols or any of the other endocrine disrupting compounds found in household products. Levels of BPA in children are typically higher than for adults. Most importantly, even tiny amounts of endocrine disrupting chemicals, including BPA, can lead to health and behavioral problems in developing children.4 For example, increasing urinary BPA levels in children are linked to an increase in behavioral regulation problems, anxiety, and hyperactivity.
The good news is that bisphenols are rapidly metabolized. If you can identify and remove sources of bisphenols from your home and diet, you can reduce your exposure.
Orthophthalates are a group of chemicals used as plasticizers – additives that make plastics more flexible. Orthophthalates can be developmental toxicants per the U.S. National Toxicology Program.5 Some common orthophthalates interfere with the production of testosterone, which can have irreversible effects on the male reproductive system. Higher exposure to certain orthophthalates has been associated with higher incidences of preterm birth; in particular, mothers who had consistently higher exposures to orthophthalates were five times more likely to experience spontaneous preterm birth (Ferguson et al 2014, JAMA Pediatrics). Preterm birth is associated with a variety of adverse health outcomes including increase in disability as young adults.6
Orthophthalates are sometimes called “everywhere chemicals” because they are so common in household products. With respect to building products, up until recently orthophthalates were prevalent in vinyl flooring. While the vinyl flooring industry has largely phased them out of new products, many homes with vinyl flooring installed before 2015 will still likely contain orthophthalate plasticizers. Orthophthalates can also be found in sealants used throughout the home. While the sealant industry is beginning to phase out these chemicals, they are still commonly used.
Similar to bisphenols, phthalates are metabolized quickly, so identifying potential sources and removing those from the home is the easiest way to reduce exposure. Possible sources include older plastic toys, cleaning products, personal care products, sealants, older vinyl flooring (pre-2018), and fragrances.
My daughter is not an outlier. Over the last 40 years, the average age of initial onset of puberty has decreased by 12 months. There are likely multiple reasons for this trend. However, an increase in exposure to a cocktail of endocrine disruptors is a possible explanation. Collectively, we can use our voices and buying power to shift the market towards safer products.
Dr. Ami Zota, Associate Professor at the Department of Environmental & Occupational Health at the George Washington University (GWU) Milken Institute School of Public Health, created a platform to amplify underrepresented voices in science and environmental health. She launched her vision, Agents of Change, in 2019 with its first cohort of changemakers.
The high-achieving crew included Dr. MyDzung Chu, a first-generation Vietnamese-American, environmental epidemiologist, new mother, and postdoctoral scientist at the GWU Milken Institute School of Public Health. MyDzung is invested in understanding social determinants of health and environmental exposures within the home, workplace, and neighborhood contexts. Her current research investigates the impact of federal housing assistance on residential environmental exposures for low-income communities.
In her Agents of Change blog, Why Housing Security is Key to Environmental Justice, MyDzung examines the intersection of housing, racism, and environmental justice, and its effects on population health. She challenges us: “It is time for the environmental health community to step up and be at the forefront of addressing housing insecurity.”
MyDzung is practicing what she preaches – and blazing a trail while doing it. In her local community, MyDzung organizes with residents and non-profit organizations for affordable housing, equitable development, and anti-displacement policies. Her dissertation research examined socio-contextual drivers of disparities in indoor and ambient air pollution and poor housing quality for low-income, immigrant, and Black and Brown households. In a study published in Environmental Research, MyDzung and colleagues found that renters in multifamily housing were exposed to higher levels of fine particulate matter indoors that homeowner households, due to a combination of building factors and source activities that may be modifiable, such as building density, air exchange, cooking, and smoking.
MyDzung has a PhD in Population Health Sciences from Harvard T.H. Chan School of Public Health, a MSPH in Environmental-Occupational Health and Epidemiology from Emory University, and a BA in Neuroscience from Smith College.
To keep up to date with MyDzung’s research and impacts, you can follow her on Twitter or LinkedIn. And, click this link to learn more about her colleagues at Agents of Change. Thanks, MyDzung, for your leadership and courage to advance real change.
Plastic is a ubiquitous part of our everyday lives, and its global production is expected to more than triple between now and 2050. According to industry projections, we will create more plastics in the next 25 years than have been produced in the history of the world so far.
The building and construction industry is the second largest use sector for plastics after packaging.1 From water infrastructure to roofing membranes, carpet tiles to resilient flooring, and insulation to interior paints, plastics are ubiquitous in the built environment.
These plastic materials are made from oil and gas. And, due to energy efficiency improvements, for example–in building operations and transportation–the production and use of plastics is predicted to soon be the largest driver of world oil demand.2
Plastic building products are often marketed in ways that give the illusion of progress toward an ill-defined future state of plastics sustainability. For the past 20 years, much of that marketing has focused on recycling. But for a variety of reasons, these programs have failed.
A recent study from the University of Michigan makes it clear that the scale of post-consumer plastics recycling in the US is dismal.3 Only about 8% of plastic is recycled, and virtually all of that is beverage containers. Further, most of the recyclate is downcycled into products of lower quality and value that themselves are not recyclable. For plastic building materials, the numbers are more dismal still. For example, carpet, which claims to have one of the more advanced recycling programs, is recycled at only a 5% rate, and only 0.45% of discarded carpet is recycled into new carpet. The rest is downcycled into other materials, which means their next go-around these materials are destined to be landfilled or burned.4 After 20 years of recycling hype, post-consumer recycling of plastic building materials into products of greater or equal value is essentially non-existent, and therefore incompatible with a circular economy.
Additives (which may be toxic), fillers, adhesives used in installation, and products made with multiple layers of different types of materials all make recycling of plastic building materials technically difficult. Lack of infrastructure to collect, sort, and recycle these materials contributes to the challenge of recycling building materials into high-value, safe new materials.
Manufacturers have continued to invest in products that are technically challenging to reuse or recycle – initially cheaper due to existing infrastructure – instead of innovating in new, circular-focused solutions. Additionally, their investment in plastics recycling has been paltry. In 2019 BASF, Dow, ExxonMobill, Shell and numerous other manufacturers formed the Alliance to End Plastic Waste (AEPW) and pledged to invest $1.5 billion over the next five years into research and development of plastic waste management technologies. Compare that to the over $180 billion invested by these same firms in new plastic manufacturing facilities since 2010.5
Globally, regulations that discourage or ban landfilling of plastics have, unfortunately, not led to more recycling overall. Instead, burning takes the place of landfilling as the eventual end of life for most plastics.
Confusing rhetoric around plastic end of life options can make this story seem more complicated than it is.6
Plastic waste burning, regardless of the euphemism employed, is a well established environmental health and justice concern.
Burning plastics creates global pollution and has environmental justice impacts.
In its exhaustive 2019 report, the independent, nonprofit Center for International Environmental Law (CEIL) documents how burning plastic wastes increases unhealthy toxic exposures at every stage of the process. Increased truck traffic elevates air pollution, as do the emissions from the burner itself. Burned plastic produces toxic ash and residue at approximately one fifth the volume of the original waste, creating new disposal challenges and new vectors of exposure to additional communities that receive these wastes.7
In the US, eight out of every 10 solid waste incinerators are located in low-income neighborhoods and/or communities of color.8 This means, in some cases, the same communities that are disproportionately burdened with the pollution and toxic chemical releases related to the manufacture of virgin plastics are again burdened with its carbon and chemical releases when it is inevitably burned at the end of its life.
The issue is global in scale. A recent report by the United Nations Environment Program (UNEP) found that “plastic waste incineration has resulted in disproportionately dangerous impacts in Global South countries and communities.” The Global Alliance for Incineration Alternatives (GAIA), a worldwide alliance of more than 800 groups in over 90 countries, has been working for more than 20 years to defeat efforts to massively expand incineration, especially in the Global South. GAIA members have identified incineration not only as an immediate and significant health threat in their communities, but also a major obstacle to resource conservation, sustainable economic development, and environmental justice.
What is unquestionable is this: Today our only choices for plastic waste are to burn or landfill most of it. Expanding plastics production and incineration is a conscious decision to perpetuate well documented, fully understood inequity and injustice in our building products supply chain.
The folks at The Story of Stuff cover this in The Story of Plastics, four minute animated short suitable for the whole family. Comedian John Oliver tells the “R-rated” version of the story with impeccable research and insightful humor in his HBO show Last Week Tonight. It’s worth a look to learn exactly how the plastics industry uses the illusion of recycling to sell ever increasing volumes of plastic. Without manufacturer responsibility and investment, efforts to truly incorporate plastic into a circular economy have little chance of success.
Coming Clean and EJHA teamed up with NRDC, Rashida Jones, and Molly Crabapple to tell the stories of vulnerable fenceline communities living near over 12,000 high-risk chemical facilities in America, urging action to protect their health and safety.
Watch ChemSec’s skit about the SIN List, to learn why hazardous chemicals should be removed from products due to the health and environmental risks they present.
In Louisiana, the factories that make the chemicals and plastics for our building products are built literally upon the bones of African Americans. Plantation fields have been transformed into industrial fortresses.
A Shell Refinery1 sprawls across the former Bruslie and Monroe plantations. Belle Pointe is now the DuPont Pontchartrain Works, among the most toxic air polluters in the state.2 Soon, the Taiwan-based Formosa Plastics Group intends to build a 2400-acre complex of 14 facilities that will transform fracked gas into plastics. It will occupy land that was formerly the Acadia and Buena Vista plantations, and not incidentally, the ancestral burial grounds of local African American residents, some of whom trace their lineage back to people enslaved there.3
Formosa has earned a reputation of being a poor steward of sacred places. Local residents have petitioned the Governor to deny permits for the facility, citing a long list of environmental health violations in its existing Louisiana facilities, including violations of the Clean Air Act every quarter since 2009.4 The scofflaw company was found to have dumped plastic pellets known as “nurdles” into the fragile ecosystem of Lavaca Bay on the Gulf of Mexico for years – leading to a record $50 million settlement with activists in that community in 2019.5
In the Antebellum South, formerly enslaved people often homesteaded on lands that were part of or near the plantations they once worked. They established communities of priceless historical and cultural worth, towns such as Morrisonville, Diamond, Convent, Donaldsonville, and St. James. Donaldsonville, Louisiana, is the town that elected Pierre Caliste Landry, America’s first African American mayor in 1868, just three years after the end of the Civil War. This part of Louisiana holds many layers of complex and deep African American history.
But in the last 75 years, since World War II, these communities have been overrun by petrochemical industry expansion enabled by governments wielding the clout of Jim Crow laws to snuff out any opposition or objection. Towns like Morrisonville and Diamond have been bought up to accommodate plant expansion. Residents have been forced to move out, their history and heritage literally paved over. It wasn’t until 1994 that the River Road African American Museum was established to preserve and present the history of the Black population as distinct from plantation representations of slavery. According to Michael Taylor, Curator of Books, Louisiana State University Libraries: “Only in the last few decades have historians themselves begun to appreciate the complexity of free black communities and their significance to our understanding not just of the past, but also the present.”6
Virtually every building product we use today contains a petrochemical component that originates from heavily polluted communities, frequently home to people of color. As the green building movement searches for ways to enhance diversity, inclusion and equity, how might it address the legacies of injustice that are tied to the products and materials we use every day?
Architect, Zena Howard, FAIA, offered insight in her 2019 J. Max Bond Lecture, Planning to Stay, keynoting the National Organization of Minority Architects national conference. Howard, known for her work on the design team for the breathtaking Smithsonian National Museum of African American History and Culture, most often works with people in communities whose culture and heritage were “erased” by urban renewal in the 1960’s. In Greenville, North Carolina, she looked to people from the historically African American Downtown Greenville community and Sycamore Hill Missionary Baptist Church Congregation to guide the planning and design process for a new town common and gateway plaza. The goal was not to “replicate” the lost community, but to bring its history and present day aspirations to life in the new design. In Vancouver, British Columbia, the development plan for a neighborhood founded by African Canadian railroad porters included an unprecedented chapter on “reconciliation and cultural redress.” The key to such efforts, according to Howard is co-creation and meaningful collaboration, whose Greek roots, she notes, mean “to labor together.”
How might we labor together to address environmental injustice when evaluating the overall healthfulness and equity of our building materials? The precedent of “insetting” suggests an approach.
Insetting has been pioneered by companies whose supply chains rely upon agricultural communities across the globe. According to Ceres, insetting is “a type of carbon emissions offset, but it’s about much more than sequestering carbon: It’s also about companies building resiliency in their supply chains and restoring the ecosystems on which their growers depend.”
In previous columns, I’ve addressed concerns about the social in industrial communities, e.g., proposals that perpetuate disproportionate pollution impacts when buying offsets rather than addressing emissions from a specific facility. Applying the “insetting” approach we might ask our materials manufacturers—and the communities that are home to the building materials industries—what steps can we take to encourage manufacturers to “labor with” communities seeking environmental justice, such as those along the Mississippi River? Can we, together, resurrect and restore their history, reconcile and redress historical wrongs, and build a healthier future for all?
To learn more about the history and present day conditions of Cancer Alley, see these excellent articles from The Guardian and Pro Publica: https://www.ehn.org/search/?q=cancer+alley
You can watch to Zena Howard’s J. Max Bond lecture, Planning to Stay, here: https://vimeo.com/378622662
You can learn more about the River Road African American History Museum here: https://africanamericanmuseum.org/
Pharos makes it easier than ever to prioritize chemicals management and identify safer alternatives to chemicals of concern. We’re excited to share several resources to help shape the next generation of green chemistry leaders:
Educators are doing important work and making our homes, workplaces and communities safer to inhabit. Pharos can help you meet your goals and streamline your work. In addition to our standard online access, now there are more ways to access chemical hazard data!
If you are interested in further details, or subscribing to Pharos, more information is available here.
ChemSec’s Marketplace connects products like this car seat with safer alternatives to hazardous chemicals, offering a platform for them to find better matches and reduce their environmental impact.
Phase 2 of this report is the first of its kind plant-by-plant accounting of the production, use, and releases of chlorine and related pollution around the world. It is intended to inform the efforts of building product manufacturers to reduce pollution in their supply chains.
Chlorine is a key feedstock for a wide range of chemicals and consumer products, and the major ingredient of polyvinyl chloride (PVC) plastic. The report includes details aboutthe production technologies used and markets served by 146 chlor-alkali plants (60 in Asia) and which of these plants supply chlorine to 113 PVC plants (52 in Asia). The report answers fundamental questions like:
Key findings include:
Supplemental Documents:
The Global Chemicals Outlook II assesses global trends and progress in managing chemicals and waste to achieve sustainable development goals, with a focus on innovative solutions and policy recommendations.