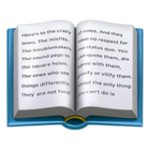
Not all recycled content materials are created equal – especially when it comes to recycled plastics.
In a report released by StopWaste and the Healthy Building Network, we take an in-depth look at the health implications, supply chain considerations, and potential to scale up recycling of the world’s most common plastic: polyethylene (aka PE). [1] This report, Post-Consumer Polyethylene in Building Products, is the latest installment in our Optimizing Recycling series.
Polyethylene is a material widely used in product packaging, beverage containers, and myriad consumer products. High Density Polyethylene (HDPE), Low Density Polyethylene (LDPE), and Linear Low Density Polyethylene (LLDPE) are all readily recyclable in California. Polyethylene plastic scrap bottles and plastic bags usually have minimal contents of concern and are easily processed into feedstock for new products, including building materials. Despite the great potential for recovery of PE, sizeable barriers stand in the way of a lot more recycling.
The explosive growth in virgin ethylene production on the U.S. Gulf Coast, driven by cheap energy, has meant that most post-consumer scrap PE is either landfilled, incinerated, or sent overseas for processing. [2]
Industry trends in recycling collection technology are also undermining the value of post-consumer polyethylene feedstocks. Pipe and plastic lumber manufacturers in the U.S. require supplies that have minimal amounts of contaminants such as volatile residual substances in packaging and other types of plastics. Yet proportionally less “good material” is coming out of the plastic waste recycling stream due to the rising use of municipal single stream recycling over the past decade. Mixed and low quality scrap materials that come from single-stream recycling centers are more likely to be exported than sorted and screened for high-quality polyethylene scrap. As a result, more recovered plastic bags are exported than processed domestically. [3]
Additives used for plastics can turn into contaminants when recycled. As seen with other recycled content materials, feedstocks with less contamination have an increased potential for recyclability as well as increased value to purchasers. [4] For PE, contaminants come in the form of residual materials from packaging (residue from bottles that contained pesticides, for example), or from additives used in manufacturing to achieve certain product characteristics. Perhaps the most problematic additive to PE products are so-called biodegradation additives used in plastic packaging. These additives (but not the rest of the plastic) degrade when exposed to sunlight or other environmental conditions. When these products are collected and used as post-consumer recycled feedstocks in products like pipes and decking, however, these additives can lower the reliability and value of a manufacturer’s product. This is why, in our report, we recommend that plastic manufacturers stop using degradability additives in all new polyethylene.