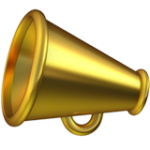
Product manufacturers, policymakers, and professionals in the building industry are paying more attention to the potential health and environmental impacts of building products during installation and use, but there has been less consideration of the important chemical impacts, including contributions to environmental injustice or environmental racism, that may occur during other life cycle stages.
Healthy Building Network (HBN) teamed up with Energy Efficiency for All (EEFA) to expand understanding of products’ life cycle health and environmental justice impacts. Together, the two organizations developed a framework based on the principles of green chemistry and the principles of environmental justice, and applied this framework to two widely-used insulation materials: fiberglass and spray polyurethane foam (SPF) insulation.
Supporting Documents:
This comprehensive guide, designed for architects, engineers, and contractors, provides expert insights, academic research, and practical advice on various aspects of piping systems, including material properties, safety considerations, health risks, environmental impacts, and emerging trends.
A study investigated the presence of per- and polyfluoroalkyl substances (PFAS) in dust from buildings with “healthier” materials, finding lower PFAS contamination levels compared to conventional buildings, highlighting the importance of using chemical class-based methods for evaluating PFAS exposure.
In this study several commercial paints were analyzed for volatile and nonvolatile per- and polyfluoroalkyl substances (PFAS), finding that paints could be potential sources of human exposure to PFAS, with one paint exceeding the reference dose for children and adults.
Project teams want buildings that are healthy for people and the planet. Two sometimes competing criteria to evaluate the sustainability of building products are embodied carbon and material health.
For this case study, Perkins&Will partnered with Healthy Building Network to identify key drivers of embodied carbon and material health by looking at specific examples of product categories frequently specified in building projects. Using flooring and drywall as examples, this study identifies some examples of where paths toward low embodied carbon and safer materials align and where they conflict.
The goal of this case study is to translate the learning from embodied carbon assessment tools and material health assessment tools into actionable guidance for manufacturers, project teams, and green building programs that will allow them to optimize decisions and promote and select healthier, low-carbon products that advance a circular economy.
Healthy Building Network (HBN) has often heard these two issues framed as a competition–a false choice. Instead, we know that these two powerhouses must work together for optimal results.
In 2022, HBN and Perkins & Will published a study highlighting building products that can do just that: optimize material health and lower their carbon footprint. This study identified key drivers and paths towards low embodied carbon and safer materials as well as when to consider and optimize both at the same time. To illustrate this point, we plotted an actionable path for project teams using flooring products as an example.
Team Low-Carbon Products: The embodied carbon of building materials contribute a whopping 11% to global carbon emissions.1 Most of these emissions happen before that product even gets installed. Additionally, the poorest countries and regions are those most impacted in terms of damage and loss of life by the effects of climate change.2 “That 11% might sound small compared with the impact of operational energy (28%), but for new construction, embodied carbon matters just as much as energy efficiency and renewables. That’s because the emissions we produce between now and 2050 will determine whether we meet the goals of the 2015 Paris climate accord and prevent the worst effects of climate change,” explains a BuildingGreen report.
Team Safer Materials: We spend 90% of our time indoors, and hundreds of industrial chemicals are found in our indoor spaces— in the dust, in the air we breathe, and in our bodies.3 The health impact of building materials are not limited to their time in use in the building, they often occur during manufacturing, installation, and at the product’s end of life. People living in close proximity to industrial facilities experience persistently worse air quality than average and exposure to industrial pollutants disproportionately impacts people of color.4 Another report suggests man-made pollution has exceeded the Earth’s safe operating boundaries.5 “Transgressing a boundary increases the risk that human activities could inadvertently drive the Earth System into a much less hospitable state, damaging efforts to reduce poverty and leading to a deterioration of human wellbeing in many parts of the world, including wealthy countries.” Professor Will Steffen, researcher at the Centre and the Australian National University, Canberra.6
Reducing toxic chemical use and the emissions associated with building materials NOW is a vital sustainability strategy for any project team.
The Research:
To identify the key drivers of embodied carbon and the key opportunities to reduce embodied carbon for each product type we read Environmental Product Declarations (EPDs), reviewed literature and data compilations, and conducted manufacturer interviews. The hazards associated with flooring products, the chemicals used to make those materials and the hazards associated with the chemicals used to install those products were collected using InformedTM product guidance and hazard data in the Pharos database.
Embodied Carbon:
Our research concluded that flooring products’ embodied carbon impacts are mostly associated with the raw material supply. The biggest opportunities to reduce embodied carbon in flooring comes from choosing a different product type that uses less impactful raw materials as well as products with longer service life. Carpet was consistently the most impactful product type due in part to its short service life. Plant-based flooring products, such as wood and natural cork, were consistently the least impactful.
Material Health:
Not surprisingly, the biggest opportunities to avoid chemicals of concern in flooring come from choosing a product type with typically fewer chemicals of concern. Products made from plastic, such as vinyl, nylon, or polyurethane tend to use more hazardous chemicals during manufacturing, installation, use, and end of life, than mineral or plant-based products. Selecting a product that is yellow or above in InformedTM color ranking Flooring Guidance, such as wood or linoleum, or even a non-vinyl resilient flooring will minimize the use of hazardous chemicals. Products in the red zone such as vinyl and carpet, should be avoided.
Conclusion:
When we looked at the opportunities to improve embodied carbon and improve material health for flooring we found that they were largely complementary.
These findings highlight the importance of pre-emptive design. Parallel to the way we conduct early modeling for energy or water use, the industry needs to model for embodied carbon and material health. A materials modeling approach–where the entire team is engaged early – before design development or construction development – will enable educated decisions before the design is set. Use HBN’s Embodied Carbon and Material health in Flooring and Drywall report and tools like Informed™ and the Carbon Smart Materials Palette to select typically healthier, low-carbon building product options.
Insulation selection has generally focused on prioritizing a product’s ability to reduce greenhouse gas (GHG) emissions from building operation, though increasingly considerations include GHG emissions from a material’s life cycle, from manufacture through disposal (known as embodied carbon).
However, this singular focus on GHGs fails to account for other harmful emissions associated with the life cycle of these materials, including toxic pollution that disproportionately burdens Black, Indigenous, people of color (BIPOC), and/or low-income communities. As billions of pounds of new insulation is being installed in buildings each year, failure to address these toxic impacts will mean that building decarbonization efforts will further entrench environmental injustice.
Healthy Building Network (HBN) joined NRDC and Energy Efficiency for All in an analysis of the life cycle chemical and environmental justice impacts of two popular building insulation materials—fiberglass and spray polyurethane foam (SPF).
The analysis found that both SPF and fiberglass release pollution into BIPOC communities over their life cycles, but SPF carries a much heavier pollution burden. The combined population surrounding the facilities that manufacture the key ingredient of SPF has almost double the percentage of Latino people compared to the U.S. overall. These facilities reported releasing an average of about 560,000 pounds of related hazardous chemicals every year and have a history of noncompliance with EPA regulations. Our previous research also found that spray foam has significant hazardous chemical concerns during installation and use in buildings.
Regarding embodied carbon, while the specifics vary, studies (such as here, here, and here) consistently show that closed cell SPF has significantly higher embodied carbon per R-value than fiberglass insulation. Further, SPF is made from almost entirely fossil fuel-derived inputs, with no recovery, reuse, or recycling of the material—necessitating continued extraction and refining of fossil fuels to produce this insulation product. Overall, comparing material health, environmental justice, and embodied carbon impacts between SPF and fiberglass, fiberglass is preferable on all accounts.
However, fiberglass manufacturing still releases hazardous pollution into communities who are disproportionately BIPOC and/or low income, and many fiberglass facilities have exhibited regular noncompliance with EPA regulations. Fiberglass manufacturers can reduce and eliminate such pollution by using less hazardous chemistries. For example, all four U.S. manufacturers reported reduced releases of formaldehyde by changing to safer binder formulations for many of their products between 2002 and 2015.
Why It Matters
As laid out in the Equitable and Just National Climate Platform:
“To achieve our [climate] goals, we will need to overcome past failures that have led us to the crisis conditions we face today. Past failures include the perpetuation of systemic inequalities that have left communities of color, tribal communities, and low-income communities exposed to the highest levels of toxic pollution and the most burdened and affected by climate change. The defining environmental crisis of our time now demands an urgency to act. Yet this urgency must not displace or abandon the fundamental principles of democracy and justice…Unless justice and equity are central components of our climate agenda, the inequality of the carbon-based economy will be replicated in the new economy.”
To truly be part of a just and equitable transition to a clean economy, climate solutions like building insulation must advance the well-being of BIPOC and low-income communities. We recommend that embodied chemical and environmental justice impacts drive material decision-making on par with consideration of GHG emissions.
Your Action Today = Healthier, More Just Future
In general, there are significant opportunities to improve the life cycle of building insulation materials through avoiding hazardous chemicals, implementing circularity, and taking other actions stemming from the principles of green chemistry and environmental justice.
Manufacturers and policymakers should advance transparency about what is in a product, how and where it is made, and the hazardous releases that occur throughout its life cycle. In the meantime, those who choose building materials can start by avoiding hazardous chemicals in a product’s content to help protect not only building occupants and installers, but also others impacted by those hazardous chemicals throughout the supply chain. Our InformedTM product guidance can help you choose safer materials.
All stakeholders–including manufacturers, policymakers, and those who choose building materials–should support the leadership of frontline communities and make changes to their own practice so that all families have healthy places to live, learn, work, and play.
We have been picking on plastics a lot recently (see articles: Addressing the Plastic Crisis: Why Vinyl Has to Go and The Illusion of Plastic Recycling: Neither Just Nor Circular). This is because we believe that typically the best way to avoid hazardous chemicals is to avoid plastic altogether. With this said, we recognize plastics in buildings are currently ubiquitous (see article: Our Plastic Buildings: A New Driver of Fossil Fuel Demand).
So, let’s consider what would need to happen for plastic building products to be considered truly sustainable. Can the plastics industry do better? What are the key opportunities today to do so, and what global policy tools could promote these opportunities? These are among the key questions HBN explored in the development of a pair of case studies for the international Organization for Economic Co-operation and Development (OECD) as part of the Inter-Organization Programme for the Sound Management of Chemicals (IOMC).
Before we jump into the case study findings, first, let’s define plastics. For the purposes of this article, we define plastics to be any polymeric material, fossil fuel based or bio-based. The case studies focused on durable plastic goods, using building materials as an example.
The case studies explored both plastic flooring and plastic insulation with the goal of increasing awareness of environmental and human health impacts of plastic product production at each stage of the lifecycle and proposing policy interventions that can help move the industry toward more sustainable plastics products in general.
In the report, we created a framework for evaluating what a truly sustainable plastic product would look like. These goals are lofty, and currently no existing plastic building materials meet these goals. However, they provide a pathway towards truly sustainable products.
To be considered a sustainable plastic, a product would have to enhance human and environmental health and safety across the entire product life cycle. It would have to be managed within a sustainable materials management system, and would have to meet the following goals:
The case study explores trade-offs that exist between different material choices.
For a flooring example, a product that is designed to use adhesive to install is typically thinner than one that uses a click tile system to install. These thinner products use less material per square foot and therefore have less chemical impacts associated with manufacturing and less waste at the end of life. However, adhesives may add hazardous substances to the product installation stage. By moving from a click tile product to a glue down product, chemical exposure burdens shift from manufacturing and end of life to the installation stage and use phase.
For an insulation example, a product that is designed to chemically react at the build site, such as spray polyurethane foam (SPF), can allow the insulation to form an air-sealed custom fit. However, SPF is not recyclable, and adherence of that insulation to surrounding materials may also make those materials more difficult to reclaim or recycle. Moving from XPS, EPS or polyiso to SPF may reduce the ability of other surrounding materials to “have a commercial afterlife” in the pursuit of an added performance feature.
Building awareness around these trade-offs enables stakeholders to make informed choices.
Now, back to reality after crafting the characteristics of a theoretical sustainable plastic. The bottom line is that there are no sustainable plastics that exist today, and we are a long way off from that day. Today, project teams need to prioritize which sustainability goals are most important and how to deal with real and significant gaps in understanding and/or data.
The case studies compared only product types made of plastic, but in reality, project teams have a wider variety of materials to choose from in any given product category. HBN’s Product Guidance considers the most commonly used product types within a product category and ranks those product types relative to one another from a chemical hazard perspective. Product types made of plant-based materials or minerals tend to rank higher than plastic products. You can apply the same sustainability goals proposed in this article to non-plastic products.
In project design, the biggest leaps towards more sustainable products from a chemicals perspective often requires consideration of vastly different materials versus making incremental improvements in chemistry for a particular product type. For example, this could mean moving from vinyl to linoleum flooring versus attempting to select the least bad vinyl option.
Check out the full flooring and insulation case studies for examples of how to use these goals to consider and choose the variety of plastic product types you will inevitably be specifying for your next project. Alternatively, challenge yourself to skip the plastics whenever possible. Even selecting one non-plastic product is cause for celebration. Make the swap!
This chapter in ILFI’s book The Regenerative Materials Economy explores the often overlooked life cycle chemical and environmental justice impacts of building materials, focusing on insulation materials like fiberglass and spray polyurethane foam (SPF).
Through a framework rooted in green chemistry and environmental justice principles, authors Rebecca Stamm of HBN and Veena Singla of NRDC analyze manufacturing realities, environmental justice concerns, and environmental health impacts, providing recommendations to improve the industry’s sustainability and reduce the negative effects on marginalized communities.
This Women’s History Month, we’re celebrating an incredible leader in the green chemistry and healthy materials space: our very own Teresa McGrath! Teresa is Habitable’s Chief Research Officer, leading our research strategies.
Prior to working at Habitable, Teresa led the Chemical Management Program for Sherwin-Williams, the largest paints and coatings company in the world, where she focused on hazards reduction and transparency and assisted business units in meeting sustainability and green chemistry goals. She also spent nine years as the Senior Managing Toxicologist at NSF International’s Green Chemistry Programs, and two years at the Environmental Protection Agency in the Design for the Environment (DfE) Branch of the Office of Pollution Prevention and Toxics (OPPT).
We caught up with Teresa to learn why she’s a champion for safer chemicals and healthier products and to get her perspective on the industry today.
HABITABLE:
What got you interested in working in sustainable products and clean chemistry?
TERESA MCGRATH:
It all starts with my family. Specifically my father – who would never identify as an environmentalist – but through his actions taught me to care for those who are most vulnerable and to take care of our planet. For example, more than once I witnessed my dad giving CPR to an injured animal that one of our dogs had mangled. In grade school I disgusted my friends by pulling carrots out of a peanut butter and jelly coated baggie my father had reused (this was before reusable bags were a thing!).
In college I did a research project on how to remove pesticides from drinking water using a biocatalytic filter method. It took me until the end of the project to ask myself “Wait, why is this pollution in our drinking water to begin with? Why are we using chemistry in such an inefficient, clumsy way?” After a little digging I stumbled on the Twelve Principles of Green Chemistry, authored by Dr. Paul Anastas and Dr. John Warner. These principles are centered around using chemistry to prevent pollution rather than create it, to make efficient use of resources down to every atom, to avoid waste. This was an inspiring moment for me.
I decided to pursue a graduate degree in chemistry that focused on Green Chemistry. At the time the only graduate program focused entirely on “Clean Chemical Technology” was in the U.K. at University of York. Off to England I went, and I have worked in the field of Green Chemistry for my entire career.
H:
What has surprised you the most about working in this field?
TM:
I have worked in government, NGOs, and industry. I think what is surprising is how much these stakeholders have in common and how most people want the same things when it comes to human health and the environment. Most people want (to make, use, or buy) safer products that work well and they can afford. It is this alignment that we can all use to make progress.
The most exciting projects in my work experience were those that harnessed input from different stakeholders with different perspectives. For example, in 2017 Valspar invited NGOs and academics who fought against the use of the endocrine-disrupting chemical bisphenol A (BPA) to help them design and test alternatives to BPA for use in food packaging.
We can all learn from each other, and these moments of collaboration are critical to enable market changes toward products that are safer for human health and the environment.
H:
Who has inspired you along your journey?
TM:
In addition to Dr. Anastas and Dr. Warner, I am grateful to Dr. Lauren Heine, who I met at a Gordon Green Chemistry conference when I was in graduate school and has been a friend and mentor to me ever since. Dr. Heine is a leader in the field of green chemistry, green engineering, and sustainable business practices.
I first met Lauren when she was the Director of Applied Science at Green Blue Institute, where she developed the CleanGredients database in partnership with the U.S. Environmental Protection Agency (EPA) to help cleaning product manufacturers find safer alternatives. At Clean Production Action, she co-authored and led the development of the GreenScreen for Safer Chemicals, a method for comparative chemical hazard assessment. She has also worked as Director of Science and Data Integrity at ChemFORWARD, where she co-created a harmonized chemical hazard assessment methodology that will not helps people avoid chemicals of concern, but also identify safer alternatives. She serves on various advisory boards and committees all over the world to share with the rest of the world a bit of the brilliance whenever she can.
Lauren taught me that collaboration is one of the most important tools to inspire change. She has an unique ability to build connections and relationships with every project she is involved with. I aspire to approach my work with this same focus.
I also credit Lauren with helping me land my very first job out of graduate school at the EPA despite the fact that I handed her a printed resume on scented paper (long story!).
H:
What are you excited about?
TM:
When I talk to project teams about how they find and select healthier products for new construction or retrofits, I often hear that they rely on disclosures like Health Product Declarations (HPDs) or Declare labels, or ecolabels such as Greenseal or Cradle to Cradle certifications, or most often they rely on manufacturer claims about the product.
I’m feeling optimistic that there has been more traction with manufacturers using these great transparency programs. There are a limited number of products on the market today that carry disclosures, and even fewer that have ecolabels. Real estate teams often feel stuck when the product they want to select is not yet disclosed. Also, because a product carries a disclosure or an ecolabel does not mean it is the best choice to avoid hazards for that product category.
I believe that there is a lot of value in disclosures and product certifications and that they play a critical role in our ecosystem. And, I believe the most powerful way to achieve safer products is to start BEFORE relying on those product disclosure tools. Project teams can take advantage of product type guidance to select products that are typically safer than others – all before ever selecting from an individual manufacturer.
Habitable’s InformedTM product guidance is informed by our 20+ years of building materials research. Guidance for individual product categories are generated by analyzing everything we know about a product category, including the way the products are made, the hazards associated with the product content, and end of life options for different product types. The reason I am so excited about this resource is that it summarizes a LOT of technical information into a simple, easy to use format that can be applied easily to both benchmark current practices and select typically safer products for projects, and even help document the powerful impacts of choosing safer materials on a project.
H:
What advice do you have for up-and-coming leaders in this space?
TM:
Don’t be afraid to reach out directly to professionals to learn more about their jobs. Ask what experience they are looking for in candidates, what their day to day looks like, and even directly ask about open positions or internship opportunities. Once you are in a role, actively look for opportunities to meet people within and outside of your organization. By expanding your network you learn different perspectives and build your capacity to collaborate on your next project. I can say from experience that you can make an impact from many different vantage points. We need young energetic leaders in NGOs, government, industry, and academia who are passionate about making the world a better place!