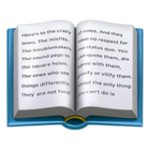
HBN and Perkins&Will have released a second report aimed at transforming the way project teams select sustainable, low-carbon products. Building on the first report titled “Embodied Carbon and Material Health in Gypsum Drywall and Flooring,” a second report investigating the intersection of carbon and material health is titled “Embodied Carbon and Material Health in Insulation”.
Insulation is a unique product category that can help reduce a building’s operational carbon emissions by optimizing performance, lowering the energy required for heating and cooling. Those same materials can also negatively impact the environment by releasing greenhouse gasses throughout their life cycle. Insulation can also contain toxic chemicals that migrate into interior spaces. This report provides guidance for designers and architects to choose the best materials that takes materials health and embodied carbon into consideration.
Key Highlights from the reports include:
The reports represent a significant step forward in sustainable design practices, offering actionable insights that empower professionals to make environmentally conscious choices without compromising on carbon or health priorities.
Project teams want buildings that are healthy for people and the planet. Two sometimes competing criteria to evaluate the sustainability of building products are embodied carbon and material health.
For this case study, Perkins&Will partnered with Healthy Building Network to identify key drivers of embodied carbon and material health by looking at specific examples of product categories frequently specified in building projects. Using flooring and drywall as examples, this study identifies some examples of where paths toward low embodied carbon and safer materials align and where they conflict.
The goal of this case study is to translate the learning from embodied carbon assessment tools and material health assessment tools into actionable guidance for manufacturers, project teams, and green building programs that will allow them to optimize decisions and promote and select healthier, low-carbon products that advance a circular economy.
Healthy Building Network (HBN) has often heard these two issues framed as a competition–a false choice. Instead, we know that these two powerhouses must work together for optimal results.
In 2022, HBN and Perkins & Will published a study highlighting building products that can do just that: optimize material health and lower their carbon footprint. This study identified key drivers and paths towards low embodied carbon and safer materials as well as when to consider and optimize both at the same time. To illustrate this point, we plotted an actionable path for project teams using flooring products as an example.
Team Low-Carbon Products: The embodied carbon of building materials contribute a whopping 11% to global carbon emissions.1 Most of these emissions happen before that product even gets installed. Additionally, the poorest countries and regions are those most impacted in terms of damage and loss of life by the effects of climate change.2 “That 11% might sound small compared with the impact of operational energy (28%), but for new construction, embodied carbon matters just as much as energy efficiency and renewables. That’s because the emissions we produce between now and 2050 will determine whether we meet the goals of the 2015 Paris climate accord and prevent the worst effects of climate change,” explains a BuildingGreen report.
Team Safer Materials: We spend 90% of our time indoors, and hundreds of industrial chemicals are found in our indoor spaces— in the dust, in the air we breathe, and in our bodies.3 The health impact of building materials are not limited to their time in use in the building, they often occur during manufacturing, installation, and at the product’s end of life. People living in close proximity to industrial facilities experience persistently worse air quality than average and exposure to industrial pollutants disproportionately impacts people of color.4 Another report suggests man-made pollution has exceeded the Earth’s safe operating boundaries.5 “Transgressing a boundary increases the risk that human activities could inadvertently drive the Earth System into a much less hospitable state, damaging efforts to reduce poverty and leading to a deterioration of human wellbeing in many parts of the world, including wealthy countries.” Professor Will Steffen, researcher at the Centre and the Australian National University, Canberra.6
Reducing toxic chemical use and the emissions associated with building materials NOW is a vital sustainability strategy for any project team.
The Research:
To identify the key drivers of embodied carbon and the key opportunities to reduce embodied carbon for each product type we read Environmental Product Declarations (EPDs), reviewed literature and data compilations, and conducted manufacturer interviews. The hazards associated with flooring products, the chemicals used to make those materials and the hazards associated with the chemicals used to install those products were collected using InformedTM product guidance and hazard data in the Pharos database.
Embodied Carbon:
Our research concluded that flooring products’ embodied carbon impacts are mostly associated with the raw material supply. The biggest opportunities to reduce embodied carbon in flooring comes from choosing a different product type that uses less impactful raw materials as well as products with longer service life. Carpet was consistently the most impactful product type due in part to its short service life. Plant-based flooring products, such as wood and natural cork, were consistently the least impactful.
Material Health:
Not surprisingly, the biggest opportunities to avoid chemicals of concern in flooring come from choosing a product type with typically fewer chemicals of concern. Products made from plastic, such as vinyl, nylon, or polyurethane tend to use more hazardous chemicals during manufacturing, installation, use, and end of life, than mineral or plant-based products. Selecting a product that is yellow or above in InformedTM color ranking Flooring Guidance, such as wood or linoleum, or even a non-vinyl resilient flooring will minimize the use of hazardous chemicals. Products in the red zone such as vinyl and carpet, should be avoided.
Conclusion:
When we looked at the opportunities to improve embodied carbon and improve material health for flooring we found that they were largely complementary.
These findings highlight the importance of pre-emptive design. Parallel to the way we conduct early modeling for energy or water use, the industry needs to model for embodied carbon and material health. A materials modeling approach–where the entire team is engaged early – before design development or construction development – will enable educated decisions before the design is set. Use HBN’s Embodied Carbon and Material health in Flooring and Drywall report and tools like Informed™ and the Carbon Smart Materials Palette to select typically healthier, low-carbon building product options.
Insulation selection has generally focused on prioritizing a product’s ability to reduce greenhouse gas (GHG) emissions from building operation, though increasingly considerations include GHG emissions from a material’s life cycle, from manufacture through disposal (known as embodied carbon).
However, this singular focus on GHGs fails to account for other harmful emissions associated with the life cycle of these materials, including toxic pollution that disproportionately burdens Black, Indigenous, people of color (BIPOC), and/or low-income communities. As billions of pounds of new insulation is being installed in buildings each year, failure to address these toxic impacts will mean that building decarbonization efforts will further entrench environmental injustice.
Healthy Building Network (HBN) joined NRDC and Energy Efficiency for All in an analysis of the life cycle chemical and environmental justice impacts of two popular building insulation materials—fiberglass and spray polyurethane foam (SPF).
The analysis found that both SPF and fiberglass release pollution into BIPOC communities over their life cycles, but SPF carries a much heavier pollution burden. The combined population surrounding the facilities that manufacture the key ingredient of SPF has almost double the percentage of Latino people compared to the U.S. overall. These facilities reported releasing an average of about 560,000 pounds of related hazardous chemicals every year and have a history of noncompliance with EPA regulations. Our previous research also found that spray foam has significant hazardous chemical concerns during installation and use in buildings.
Regarding embodied carbon, while the specifics vary, studies (such as here, here, and here) consistently show that closed cell SPF has significantly higher embodied carbon per R-value than fiberglass insulation. Further, SPF is made from almost entirely fossil fuel-derived inputs, with no recovery, reuse, or recycling of the material—necessitating continued extraction and refining of fossil fuels to produce this insulation product. Overall, comparing material health, environmental justice, and embodied carbon impacts between SPF and fiberglass, fiberglass is preferable on all accounts.
However, fiberglass manufacturing still releases hazardous pollution into communities who are disproportionately BIPOC and/or low income, and many fiberglass facilities have exhibited regular noncompliance with EPA regulations. Fiberglass manufacturers can reduce and eliminate such pollution by using less hazardous chemistries. For example, all four U.S. manufacturers reported reduced releases of formaldehyde by changing to safer binder formulations for many of their products between 2002 and 2015.
Why It Matters
As laid out in the Equitable and Just National Climate Platform:
“To achieve our [climate] goals, we will need to overcome past failures that have led us to the crisis conditions we face today. Past failures include the perpetuation of systemic inequalities that have left communities of color, tribal communities, and low-income communities exposed to the highest levels of toxic pollution and the most burdened and affected by climate change. The defining environmental crisis of our time now demands an urgency to act. Yet this urgency must not displace or abandon the fundamental principles of democracy and justice…Unless justice and equity are central components of our climate agenda, the inequality of the carbon-based economy will be replicated in the new economy.”
To truly be part of a just and equitable transition to a clean economy, climate solutions like building insulation must advance the well-being of BIPOC and low-income communities. We recommend that embodied chemical and environmental justice impacts drive material decision-making on par with consideration of GHG emissions.
Your Action Today = Healthier, More Just Future
In general, there are significant opportunities to improve the life cycle of building insulation materials through avoiding hazardous chemicals, implementing circularity, and taking other actions stemming from the principles of green chemistry and environmental justice.
Manufacturers and policymakers should advance transparency about what is in a product, how and where it is made, and the hazardous releases that occur throughout its life cycle. In the meantime, those who choose building materials can start by avoiding hazardous chemicals in a product’s content to help protect not only building occupants and installers, but also others impacted by those hazardous chemicals throughout the supply chain. Our InformedTM product guidance can help you choose safer materials.
All stakeholders–including manufacturers, policymakers, and those who choose building materials–should support the leadership of frontline communities and make changes to their own practice so that all families have healthy places to live, learn, work, and play.
Simona Fischer, MSR Design
As registered architect, sustainable design professional, and associate with MSR Design, Simona Fischer has spent much of her career thus far developing and testing strategies for integrating sustainable design into the workflow of architectural practice. Her experience includes project management, Living Building Challenge documentation, and firmwide sustainable design implementation.
Simona is a dynamic community of practitioners who help co-create solutions to accelerate the adoption of healthier building materials in affordable housing. She has presented at national conferences, lectures regularly at the University of Minnesota, and currently co-chairs the AIA Minnesota Committee on the Environment (COTE).
Simona was instrumental in the Living Building Challenge Petal Certification of MSR Design’s new downtown Minneapolis headquarters, which achieved the materials, beauty, and equity petals. The project incorporated more than 114 Red List Free materials and achieved a 28 percent reduction of its embodied carbon footprint by using salvaged materials. She also led the development of guidelines around transparency, sustainability, and health for the firm’s materials library, including training materials for staff and external sales reps.
We sat down with Simona to learn why materials have been a focus of her career and to get her perspective on the green building industry today.
What sparked your passion about healthier materials? Was there an “aha” moment or a time that something just clicked?
I was that kid who won a prize for designing the elementary school recycling banner, so I guess I’ve cared about materials for a long time. But my interest in building materials was piqued in architecture school, when we were challenged to create a new ecolabel. Faced with inventing a way to compare one material to another in terms of sustainability, I realized how mind-blowingly complex of a task that was. How do you make the criteria objective? How do you compare products across categories? How do you measure health – is it just by the list of ingredients, or do you include research on health outcomes factoring exposure and risk (and if so, what research even exists)? How do you stack human health and other metrics against each other and choose which factor outweighs the other? How do you account for performance and durability? The questions were endless and led to more questions, which I found complex and intriguing. In other topic areas like water and energy in buildings, the goal seemed straightforward (at least on the surface). Use less energy, and make it cleaner. Use less water, and make it cleaner. But with materials, the number of variables were infinite. We had to think about balancing not just toxicity to people and embodied carbon, but also harvesting of raw materials, ethical manufacturing, and what to do with all that stuff at the end of its useful life.
I ended up writing my MS thesis on methods for assessing sustainability at the level of the manufacturer, as opposed to focusing solely on individual products which change so frequently. I was really just trying to find a system map at a higher level, and make the big, shifting world of materials more manageable in my head. I still use some of what I learned during that project as indicators of whether a building product manufacturer is serious about human health and sustainability, or just greenwashing. But sometimes they are greenwashing because they don’t know any better, and they are on their way to improving. So you can’t just write off smaller companies who don’t yet have all the documentation. It’s a learning process for them as well.
At MSR Design, the conversation about healthy materials had already started when I joined to work on The Rose, a Living Building-inspired affordable housing development in Minneapolis. My colleagues Rhys MacPherson, Paul Mellblom, and Rachelle Schoessler-Lynn were leading the conversation about why we should, and how we could, avoid vinyl and other chemicals on The Rose and on other projects across the firm. Over the next couple years we held a number of all-staff discussions and training sessions on healthy materials. Many staff members, from seasoned designers to interns, became interested in the question of how we could do better while still delivering a beautiful aesthetic and the best functionality for our clients. By the time we were ready to start designing our new studio, healthy materials as a concept had had enough time to become embedded in the culture
Tell us about your project to build the new MSR studio. Why was it important to prioritize healthy materials for this project? What went into your process?
When we knew we were moving, we held an all-staff discussion to debate frameworks for certification. We considered LEED, WELL, Fitwell, and Living Building Challenge Petal Certification. In the end, LBC won, because the Materials Petal was so ambitious, prioritizing not only human health through the use of Red List Free products, but also environmental health and other butterfly-effect impacts of resource harvesting and global warming potential and waste. At the same time, the LBC path included an emphasis on equity, as well as using the project as a tool to educate and inspire others. We found the holistic approach inspiring, and appreciated the challenge (most days).
It was important to prioritize healthy materials because we knew our staff cared about living out our values around healthy indoor environments. I think the team will agree that meeting the Red List requirement was difficult. It took time to develop a workflow for gathering the documentation. But it also gave us the opportunity to rethink the way we approach materials from the start of projects. Instead of trying to weed out all the “bad” chemistry, we found it was actually easier to start from scratch and build up a list of materials we knew were likely to comply with the requirement. It ended up being simpler, mostly natural materials, which we used as the palette for our space.
How do you consider low embodied carbon versus health in product selection?
Non-toxic materials and low embodied carbon are two lenses on a singular problem, which is planetary health. Human health is a subcategory of planetary health, since we’re part of the planet and made of its stuff. When indoor and outdoor environments, and plant and animal and human bodies, are polluted by toxic substances, both from human-made toxins and an overabundance of greenhouse gasses, the global ecosystem suffers and humans suffer within it. We are nature. What’s interesting is, younger, upcoming professionals and design students seem to understand this intuitively. They don’t even need to be told that human and global environmental health go hand in hand. So I think as an industry, we just need to accept the interplay of embodied carbon and human health as a foregone conclusion and get straight to the nitty-gritty of what materials we use and how those materials are grown, produced, manufactured and delivered.
That said, we also need to get serious about the data used to back up carbon and health claims. We need transparent, standardized reporting from manufacturers, including making sure the scope of every life cycle assessment (LCA) takes all the impact categories of the AIA Materials Pledge into account. I think petroleum-based building materials are going to be a battleground for a while to come. The low purchase price and saturation in the market make plastics seem like an easy choice for all kinds of different finishes and performance layers in buildings. It is possible to make them somewhat healthier for end-users by being careful to avoid certain additives. But that leaves a massive loophole; the impacts of production and waste on planetary health. I think there’s an opportunity for data to drive a new understanding here. If we can start seeing standardized collection and data crunching of environmental product declaration (EPD) data from different product sectors, we might be able to correlate carbon from building products more directly to regional health impacts of the production of those chemistries. This would help close loopholes that allow the incredible health impact of high global warming potential (GWP) emissions to stay hidden in the shadows
How have you used your knowledge to help move your clients toward healthier materials? What has been most successful?
I think some of my most successful work has been in addressing priorities and processes in our workflow. I can’t count the number of times I’ve heard people say they just wish there was a single, simple database of all the great products. There are ever-improving databases out there, but people always want something else that is missing, so the problem hasn’t been solved. I think the missing piece is a deeper understanding of the principles of product categories, such as knowing what different types–not brands, but general types–of insulation or countertop materials are made of, and where they come from. This level of knowledge, over time, becomes a kind of intuition one uses to filter the world of products even as new things constantly appear in your inbox or your lunch and learns. When you understand the principles, and don’t just rely on a database to provide a solution, it also gets easier to speak knowledgeably and make solid recommendations to clients.
On project work, I have the best luck when I’m upfront about why we need to consider material health alongside cost. You have to tailor your message to the audience, for example, some clients are most receptive to the idea of improving their impact on the world, whereas for others, the message that hits home is one of directly affecting their health or the health of people they care about
How has Habitable’s InformedTM building product research been helpful or influential?
I love InformedTMand recommend it to designers all the time, and clients too. The information is organized in terms of product categories as opposed to brand names or labels, so it aligns with the level of learning that I think is most beneficial to becoming smarter in practice. We used the sample specs to rewrite our paint specifications in 2021. We’ve also heard great lectures from Habitable research team members over the years that have left an impact on our staff.
What advice do you have for other AEC leaders? Are there processes or approaches you would recommend? Where would you recommend a newcomer to healthier materials start?
For designers, I recommend signing the AIA Materials Pledge and studying the categories. The Pledge is a great framework – if you address each of the Pledge categories in some way, you know you’re hitting the right bases. If you can, allot some time to staff education and discussion. I recommend the Living Building Challenge Materials Petal as a particularly inspiring framework for education and good discussion, because it is based on absolute goals, instead of relative improvement. The COTE Super Spreadsheet (downloadable on the AIA website) is a good starting point for addressing materials issues in an applied manner on projects.
At MSR Design, our internal education efforts led to the development of our Material Library Entry Criteria. If others want to design similar criteria for their libraries, they are welcome to copy ours outright or modify as needed: www.msrdesign.com/generative-impacts.
The more we as designers align in our message to manufacturers about health and carbon, the easier it becomes for them to stay in business while giving us what we want
What are you most excited about right now?
I’m excited about natural and biobased materials. On the high-tech side, there is so much opportunity for new materials to be developed, especially bio-based polymers. On the other hand, there is a new straw bale project that is being built in Minneapolis. It’s low tech in comparison to the latest research in biomaterials, and yet it combines healthy, natural materials seamlessly with low carbon construction. The team is using Passive House building science principles to build a durable system, which they will test with sensors in the walls over the next few years. I really resonate with the idea that we can build a sustainable future with natural materials in both high- and low-tech ways
What do you want other people to know?
We, as an industry, are practicing architecture and construction in an era where buildings are made of hybrid material systems so complex, we hardly know what’s in them or why they work. I think we architects can perhaps find evidence of the Vitruvian virtues of utilitas (utility) and venustas (beauty) in the work we produce, but somewhere as a profession, I think we have let go of the firmitas (stability). Not in the sense of solid structure, but in the sense of owning materiality and material knowledge as a critical aspect of an architect’s role. We have become accustomed to accepting a level of vagueness about assemblies and their tons of little components, and leaving the details to the product manufacturer. I think understanding materials deeply is about reclaiming this knowledge, and a piece of architecture we have lost
Thank you to Simona and MSR design for being leaders in healthier materials! To learn more about the MSR headquarters project, check out this case study. You can also learn more about MSR’s commitment to sustainable design and download their Sustainable Materials Action Packet on their website. Follow this link to learn more about InformedTM, product guidance which Simona mentions influencing her practice.
What do building materials have to do with social justice? Learn more in this article by Diana Alley, Avideh Haghighi, and Lona Rerickat at ZGF Architects.
Dr. Jonathan Foley, Executive Director of Project Drawdown, talks about how carbon offsets and “net zero emissions” claims are a dangerous distraction to meaningful climate change initiatives.
This report discusses how President Biden’s Executive Orders need to go further than examining energy sources to combat the climate crisis, emphasizing the need for the chemical industry to adapt and innovate, considering its significant impact on greenhouse gas emissions and environmental health.
In Louisiana, the factories that make the chemicals and plastics for our building products are built literally upon the bones of African Americans. Plantation fields have been transformed into industrial fortresses.
A Shell Refinery1 sprawls across the former Bruslie and Monroe plantations. Belle Pointe is now the DuPont Pontchartrain Works, among the most toxic air polluters in the state.2 Soon, the Taiwan-based Formosa Plastics Group intends to build a 2400-acre complex of 14 facilities that will transform fracked gas into plastics. It will occupy land that was formerly the Acadia and Buena Vista plantations, and not incidentally, the ancestral burial grounds of local African American residents, some of whom trace their lineage back to people enslaved there.3
Formosa has earned a reputation of being a poor steward of sacred places. Local residents have petitioned the Governor to deny permits for the facility, citing a long list of environmental health violations in its existing Louisiana facilities, including violations of the Clean Air Act every quarter since 2009.4 The scofflaw company was found to have dumped plastic pellets known as “nurdles” into the fragile ecosystem of Lavaca Bay on the Gulf of Mexico for years – leading to a record $50 million settlement with activists in that community in 2019.5
In the Antebellum South, formerly enslaved people often homesteaded on lands that were part of or near the plantations they once worked. They established communities of priceless historical and cultural worth, towns such as Morrisonville, Diamond, Convent, Donaldsonville, and St. James. Donaldsonville, Louisiana, is the town that elected Pierre Caliste Landry, America’s first African American mayor in 1868, just three years after the end of the Civil War. This part of Louisiana holds many layers of complex and deep African American history.
But in the last 75 years, since World War II, these communities have been overrun by petrochemical industry expansion enabled by governments wielding the clout of Jim Crow laws to snuff out any opposition or objection. Towns like Morrisonville and Diamond have been bought up to accommodate plant expansion. Residents have been forced to move out, their history and heritage literally paved over. It wasn’t until 1994 that the River Road African American Museum was established to preserve and present the history of the Black population as distinct from plantation representations of slavery. According to Michael Taylor, Curator of Books, Louisiana State University Libraries: “Only in the last few decades have historians themselves begun to appreciate the complexity of free black communities and their significance to our understanding not just of the past, but also the present.”6
Virtually every building product we use today contains a petrochemical component that originates from heavily polluted communities, frequently home to people of color. As the green building movement searches for ways to enhance diversity, inclusion and equity, how might it address the legacies of injustice that are tied to the products and materials we use every day?
Architect, Zena Howard, FAIA, offered insight in her 2019 J. Max Bond Lecture, Planning to Stay, keynoting the National Organization of Minority Architects national conference. Howard, known for her work on the design team for the breathtaking Smithsonian National Museum of African American History and Culture, most often works with people in communities whose culture and heritage were “erased” by urban renewal in the 1960’s. In Greenville, North Carolina, she looked to people from the historically African American Downtown Greenville community and Sycamore Hill Missionary Baptist Church Congregation to guide the planning and design process for a new town common and gateway plaza. The goal was not to “replicate” the lost community, but to bring its history and present day aspirations to life in the new design. In Vancouver, British Columbia, the development plan for a neighborhood founded by African Canadian railroad porters included an unprecedented chapter on “reconciliation and cultural redress.” The key to such efforts, according to Howard is co-creation and meaningful collaboration, whose Greek roots, she notes, mean “to labor together.”
How might we labor together to address environmental injustice when evaluating the overall healthfulness and equity of our building materials? The precedent of “insetting” suggests an approach.
Insetting has been pioneered by companies whose supply chains rely upon agricultural communities across the globe. According to Ceres, insetting is “a type of carbon emissions offset, but it’s about much more than sequestering carbon: It’s also about companies building resiliency in their supply chains and restoring the ecosystems on which their growers depend.”
In previous columns, I’ve addressed concerns about the social in industrial communities, e.g., proposals that perpetuate disproportionate pollution impacts when buying offsets rather than addressing emissions from a specific facility. Applying the “insetting” approach we might ask our materials manufacturers—and the communities that are home to the building materials industries—what steps can we take to encourage manufacturers to “labor with” communities seeking environmental justice, such as those along the Mississippi River? Can we, together, resurrect and restore their history, reconcile and redress historical wrongs, and build a healthier future for all?
To learn more about the history and present day conditions of Cancer Alley, see these excellent articles from The Guardian and Pro Publica: https://www.ehn.org/search/?q=cancer+alley
You can watch to Zena Howard’s J. Max Bond lecture, Planning to Stay, here: https://vimeo.com/378622662
You can learn more about the River Road African American History Museum here: https://africanamericanmuseum.org/
It is critical that these efforts align their goals lest, once again, the latest definition and marketing of “green” building products overlooks and overrides the interests of the front line communities most impacted by both climate change and toxic pollution.
The Carbon Leadership Forum describes embodied carbon as “the sum impact of all the greenhouse gas emissions attributed to the materials throughout their life cycle (extracting from the ground, manufacturing, construction, maintenance and end of life/disposal).2 In a widely praised book, The New Carbon Architecture3, Bruce King explains clearly why reducing carbon inputs to building materials immediately—present day carbon releases—is more effective at meeting urgent carbon reduction goals than the gains of even a Net Zero building, which are realized over decades. This approach is embraced by the Materials Carbon Action Network, a growing association of manufacturers and others, which states as its aim “prioritization of embodied carbon in building materials.”(emphasis added).4
Climate action priorities are framed differently by groups at the forefront of movements for climate justice and equity in the green building movement. Mary Robinson, past President of Ireland, UN High Commissioner on Human Rights and UN Special Envoy on Climate Change, says climate justice “insists on a shift from a discourse on greenhouse gases and melting ice caps into a civil rights movement with the people and communities most vulnerable to climate impacts at its heart.” 5 The Equitable and Just National Climate Platform6, adopted by a broad cross section of environmental justice groups and national organizations including Center for American Progress, League of Conservation Voters, Natural Resources Defense Council, and Sierra Club, calls for “prioritizing climate solutions and other policies that also reduce pollution in these legacy communities at the scale needed to significantly improve their public health and quality of life.” The NAACP’s Centering Equity In The Sustainable Building Sector (CESBS)7 initiative advocates “action on shutting down coal plants and other toxic facilities at the local level, as well as building of new toxic facilities, with advocacy to strengthen development, monitoring, and enforcement of regulations at federal, state, and local levels. Also includes a focus on corporate responsibility and accountability.”8
The embodied carbon and climate justice initiatives are aligned when carbon reductions in building products are achieved through industrial process changes that reduce the use of fossil fuels and other petrochemicals. But rarely, if ever, can building products be manufactured with no carbon footprint, i.e. without fossil fuel inputs. These initiatives may not be aligned when manufacturers promote “carbon neutral” or “carbon negative” products that rely on carbon trading or offsets, the practice of supporting carbon reduction elsewhere (by planting trees or investing in renewable energy) to offset fossil fuel and petrochemical inputs at the factory. According to the Equitable and Just National Climate Platform: “ . . . these policies do not guarantee emissions reduction in EJ communities and can even allow increased emissions in communities that are already disproportionately burdened with pollution and substandard infrastructure.” They may also allow increased toxic pollution, if a manufacturer chooses to invest in carbon offsets, for example, rather than invest in process changes that reduce toxic chemical use or emissions. As a result, disproportionate impacts, often correlated with race, can be perpetuated.
Vinyl provides one example of such inequity. Vinyl’s carbon footprint includes carbon tetrachloride, a chemical released during chlorine production that is simultaneously highly toxic, ozone depleting, and a global warming gas 1,400 times more potent than CO2. Offsetting these releases with tree planting or renewable energy purchases does nothing for the toxic fallout, from carbon tetrachloride, fossil fuels and other petrochemicals, on the communities adjacent to those manufacturing facilities.
Experts agree that the most embodied carbon reductions by far are to be had in addressing steel and concrete in buildings. Beyond that, experts disagree about the strength of the data available to track carbon reductions and compare products in a meaningful, objective way, and warn of diminishing returns relative to the investment needed to track carbon in every product. These may prove to be worth pursuing, but not at the expense of meaningful improvements to conditions in fenceline communities.
Habitable believes that these approaches can be reconciled and aligned through dialogue that includes the communities most impacted by the petrochemical infrastructure that is driving climate change. Our chemical hazard database, Pharos, and our collaboration with ChemFORWARD provide manufacturers with the ability to reduce their product’s carbon and toxic footprints.
We can in good faith pursue reductions in embedded carbon and toxic chemical use, climate and environmental justice and to define climate positive building products accordingly. Prioritizing selection of products simply upon claims of carbon neutrality, however, is not yet warranted.