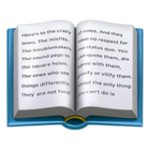
What do building materials have to do with social justice? Learn more in this article by Diana Alley, Avideh Haghighi, and Lona Rerickat at ZGF Architects.
Phase 2 of this report is the first of its kind plant-by-plant accounting of the production, use, and releases of chlorine and related pollution around the world. It is intended to inform the efforts of building product manufacturers to reduce pollution in their supply chains.
Chlorine is a key feedstock for a wide range of chemicals and consumer products, and the major ingredient of polyvinyl chloride (PVC) plastic. The report includes details aboutthe production technologies used and markets served by 146 chlor-alkali plants (60 in Asia) and which of these plants supply chlorine to 113 PVC plants (52 in Asia). The report answers fundamental questions like:
Key findings include:
Supplemental Documents:
Home Depot, the world’s largest home improvement retailer, announced Sept. 17 that it will phase out the sale of all carpets and rugs containing PFAS chemicals, expanding the reach of its Chemical Strategy adopted in 2017.
The company said it will stop purchasing for distribution in the U.S., Canada and online any carpets or rugs containing PFAS chemicals by the end of 2019. The new policy has important implications beyond reducing the use of these chemicals, which are associated with serious health harm and last virtually forever in the environment.
Environmental justice & equity: As with the 12 chemicals banned under its original 2017 Chemicals Strategy, this policy makes important strides toward equity in the green building movement. Because it impacts products at all price points, not just premium products and not just those that qualify for the retailer’s Eco-Options program, the policy ensures that all contractors and do-it-yourself customers get healthier products regardless of the brand purchased, and regardless of whether or not the product has been certified “green.” This makes it easier to implement recommendations such as those Habitable provides through our Informed™ approach.
Market Influence
A similar policy change led by the retailer in 2015, banning phthalates from all vinyl flooring it sells, was quickly adopted by all other major retailers such as Lowes, Menards, and Lumber Liquidators. Similarly, when Lowes led the industry in banning the sale of deadly paint strippers in May, 2018, its major competitors followed suit within months
Class approach to chemicals
PFAS refers to a class of nearly 15,000 that repel liquids and resist sticking, including well-known brands such as Teflon, Gore-Tex, Stainmaster and Scotchgard. Many brands have stopped using the most well studied, “long-chain” compounds in this class, but continue to use less studied “short-chain” compounds, causing confusion for consumers. Independent scientists agree that a commitment to avoiding all PFAS is the right approach for consumers and the overall environment.
Widespread PFAS Contamination of the Environment Is a Growing Concern. The Environmental Working Group (EWG) has identified over 700 sites where PFAS were detected and cited federal data suggesting that up to 110 million Americans may have PFAS in their drinking water.1 HBN’s analysis of chlorine and PVC production documented unexpectedly high use of PFAS as an alternative to mercury- and asbestos-based chlorine manufacturing technology, raising new concerns about the role of chlorine-based products and the growing concern over global PFAS exposures. The chemical industry argues that only a few of these compounds have been found unsafe, and all others should be presumed innocent until proven guilty. In 2019, 3M company launched a major public relations blitz2 to this effect, including a “PFAS Facts” website advocating that “Each PFAS compound needs to be evaluated based upon its own properties,”3 a process that would take federal regulators, at best, many decades to complete. EWG published a thorough refutation of 3M’s claims,4 and more than 250 independent scientists5 have called upon companies and regulators to stop producing and using PFAS except in the most essential applications. The Home Depot’s new carpet and rug policy, which we hope will soon be extended to other products including spray-on upholstery protection, such as 3M’s Scotchgard, follows this recommended class approach.
The Home Depot’s new policy commitment comes just two months before the release of the 2019 “Who’s Minding the Store?” Retailer Report Card, from the Mind the Store campaign, a nationwide coalition that challenges retailers to eliminate toxic chemicals and substitute safer alternatives. HBN is a coalition member and advised The Home Depot on its 2017 Chemical Strategy. The annual Report Card benchmarks retailers on their safer chemicals policies and implementation programs. The Home Depot earned a B- on the scorecard.
To learn more about PFAS and how to avoid them, watch the documentary The Devil You Know, available on all streaming services, and check out the new PFAS Central website, a project of our partners at the Green Science Policy Institute.
Phase 1 of this report is the first of its kind plant-by-plant accounting of the production, use, and releases of chlorine and related pollution around the world. It is intended to inform the efforts of building product manufacturers to reduce pollution in their supply chains.
Chlorine is a key feedstock for a wide range of chemicals and consumer products, and the major ingredient of polyvinyl chloride (PVC) plastic. The report includes details about the largest 86 chlor-alkali facilities and reveals their connections to 56 PVC resin plants in the Americas, Africa and Europe. (The second phase of this project will inventory the industry in Asia.) A substantial number of these facilities, which are identified in the report, continue to use outmoded and highly polluting mercury or asbestos.
Demand from manufacturers of building and construction products now drives the production of chlorine, the key ingredient of PVC used in pipes, siding, roofing membranes, wall covering, flooring, and carpeting. It is also an essential feedstock for epoxies used in adhesives and flooring topcoats, and for polyurethane used in insulation and flooring.
Key findings include:
Supplemental Documents:
While attending a 2018 meeting of U.S. EPA’s National Environmental Justice Advisory Council (NEJAC) in Boston, I heard the testimony of Delma and Christine Bennet. They live in Mossville, LA, amidst what is likely the nation’s largest concentration of PVC (polyvinyl chloride) manufacturing facilities. I was there to present the findings of HBN’s inventory of pollution associated with the chlorine/PVC supply chain.
Our study found, among other things, that the Gulf Coast region (which includes Mossville) is home to nine facilities that use outmoded asbestos technology, and home also to some of the industry’s worst polluters: Five of the six largest emitters of dioxins––a long lasting, extremely toxic family of hazardous waste that causes cancer and many other health impacts, are located there. The Bennets reminded the EPA that according to studies by a division of the Centers for Disease Control, Mossville residents have three times higher levels of dioxin in their blood than average Americans, and the dioxin levels found in their yards and attic dust exceed regulatory standards typically used for toxic waste remediations of industrial sites. Even the vegetables in their gardens tested positive for dioxin.
When I think about why we fight so hard to exclude PVC from any palette of green, healthy, or sustainable building materials, I think first of people like Delma and Christine. I then think about the many non-profits, government agencies, and private enterprises dedicated to recycling. Way back in the 1990’s, the industry Association of Plastic Recyclers declared PVC a contaminant to the recycling stream. A generation later, a 2016 study by the Circular Economy evangelist Ellen MacArthur Foundation called out PVC packaging for global phase-out, citing low recycling rates and chemical hazard concerns. Much of the concern about PVC packaging is driven by worries about ocean pollution. HBN’s study found that at least one U.S. PVC manufacturer is routinely dumping tons of PVC pellets into local waterways and refusing to stop even after being ordered to do so by the state of Texas.
The list goes on. Our report documents the types of industrial pollution in addition to dioxin that could be reduced or avoided by a switch to more recyclable plastics that are not made with the chlorine that is an essential ingredient of PVC, including ozone depleting and potent global warming gasses. HBN’s earlier studies have documented the hazards posed by legacy pollutants that are returning to our consumer products in recycled PVC content––heavy metals such as lead, and endocrine-disrupting plasticizers known as phthalates.
There is virtually no use of PVC in building products that could not be replaced with another plastic or other material. Indeed, from siding, to wallpaper, to window frames, PVC has displaced materials that are more recyclable, such as aluminum and paper. Because the industry is not held accountable for the environmental health damages wrought in places like Mossville, PVC has artificially low costs that present barriers to entry, or inhibit market expansion of less hazardous, more sustainable alternatives.
That is why PVC should not be part of any building, or any building rating system, that claims to advance environmental and health objectives. It’s not green. It’s not healthy. It’s not sustainable. It’s just cheap––for us. Because folks like Delma and Christine Bennet pay the true cost.
Know Better
Learn more about the implications of chlorine as a feedstock in plastics in HBN’s Chlorine and Building Materials report.
As noted in Healthy Building Network’s(HBN) Chlorine and Building Materials report, chlorine production is a major source of releases of carbon tetrachloride, a potent global warming and ozone depleting gas as well as a carcinogen.
As the report reminds us, it’s important to consider not only the use-phase impacts of building products, but the entire life cycle, including primary chemical production that’s several steps back from final product manufacture.
Blowing agents are used in plastic foam insulation to create the foam structure and also contribute to the insulative properties. Over the years, manufacturers have cycled through a range of fluorocarbons as each prior class is phased out due to environmental concerns – from ozone depleting chlorofluorocarbons (CFCs) to less ozone depleting hydrochlorofluorocarbons (HCFCs) to the non-ozone depleting but high global warming potential hydrofluorocarbons (HFCs) currently common in many types of foam insulation. Manufacturers have now begun the latest shift to next generation, low global warming potential hydrofluoroolefins (HFOs). For extruded polystyrene (XPS), this translates to a shift from commonly used HFC-134a with a global warming potential (GWP) of 1,430 to HFO-1234ze with a GWP of six.2
The summary of these chemical transitions only tells part of the story. While HFOs do not directly deplete the ozone layer or significantly contribute to global warming, many HFOs use carbon tetrachloride (CCl4) as a chemical feedstock. This includes HFO-1234ze, the replacement for HFC-134a (which does not use CCl4) in many applications.3
How is it that this ozone depleting substance is still in use? Many uses of carbon tetrachloride were phased out in 1995, under the terms of the Montreal Protocol to protect the ozone layer. But the Montreal Protocol phase-outs exempted the use of CCl4 as a chemical feedstock, under the assumption that emissions would be minor.4 However, carbon tetrachloride “is not decreasing in the atmosphere as rapidly as expected” based on its known lifetime and emissions, according to a 2016 report on the Mystery of Carbon Tetrachloride. The authors of this report concluded that emissions of carbon tetrachloride during its production, and fugitive emissions from its use as a chemical feedstock, have been significantly unreported and underestimated.5
Production of carbon tetrachloride is likely to increase as industry replaces HFC blowing agents (and refrigerants), most of which aren’t produced with carbon tetrachloride, with HFOs that do use CCl4 as a feedstock.[6] With increased production and use of carbon tetrachloride, increased emissions are expected – and that’s bad news for the earth’s recovering ozone layer.
We recommend against the use of plastic foam insulation whenever possible, but if you do use it, some products are available that use other, less impactful, blowing agents, including hydrocarbons and water. For more recommendations about preferable insulation from a health hazard perspective, review our product guidance at informed.habitablefuture.org.
Research from Healthy Building Network (HBN) documents how vinyl building products, also known as PVC or polyvinylchloride plastic, are the number one driver of asbestos use in the US.
The vinyl/asbestos connection stems from the fact that PVC production is the largest single use for industrial chlorine, and chlorine production is the largest single consumer of asbestos in the US. [1] More than 70% of PVC is used in building and construction applications – pipes, flooring, window frames, siding, wall coverings and membrane roofing. [2] This makes the building and construction industry the single largest product sector consuming chlorine, bearing sizeable responsibility for the ongoing demand for asbestos. [3]
Despite the existence of asbestos (and mercury) free chlorine production methods, the PVC industry has positioned itself at the vanguard of industry efforts to frustrate stronger asbestos regulation. According to Mike Belliveau, the Executive Director of the Environmental Health Strategy Center and a senior advisor to Safer Chemicals Healthy Families coalition, “The PVC market has spurred chemical industry lobbyists to urge the Trump Administration to exempt their use of deadly asbestos from future restrictions.” The last time the vinyl industry positioned themselves so publicly on the other side of common sense, they were defending the use of lead in children’s vinyl lunch boxes.
The health hazards of asbestos exposure, painful and deadly lung diseases including cancer, are clear. Green building professionals do not have to wait. Do your part to prevent asbestos-related diseases here and abroad. Don’t specify vinyl building products.
1. In the US more than half of chlorine is produced using asbestos, despite the availability of an alternative production method that does not require either asbestos or mercury.
2. http://www.vinylinfo.org/vinyl/uses
3. According to IHS Markit, “A majority of chlor-alkali capacity is built to supply feedstock for ethylene dichloride (EDC) production. EDC is then used to make vinyl chloride (VCM) and subsequently used to manufacture polyvinyl chloride (PVC). This chain, EDC to VCM to PVC, is normally called the vinyl chain. PVC demand correlates closely with construction spending, therefore, it can be concluded that chlorine consumption and production are driven by the construction industry. Hence, chlorine consumption growth depends on the growth of the global economy, since a country will spend more on construction if it has a healthy gross domestic product.” (IHS Markit. “Chemical Economics Handbook: Chlorine/Sodium Hydroxide (Chlor-Alkali),” December 2014. https://www.ihs.com/products/chlorine-sodium-chemical-economics-handbook.html)
4. Fifteen chlor-alkali plants last reported to be using asbestos diaphragms include, in order of estimated chlorine capacity:
5. Carpentier, Steve. “Minaçu, a cidade que respira o amianto.” CartaCapital, May 21, 2013. http://www.cartacapital.com.br/sustentabilidade/minacu-a-cidade-que-respira-o-amianto-8717.html
PVC manufacturing consumes in excess of 40 per cent of the chlorine gas produced in this country, making it the nation’s single largest user of the deadly chemical. By comparison, 5 percent of the nation’s chlorine gas is used to disinfect water – and that includes sewage treatment.
Chlorine gas kills and maims in a manner so heinous that it was banned as a chemical weapon after the battlefield experiences of World War I. Today, according to the Washington Post, anti-terrorist experts say there is “little doubt that plants storing large amounts of chlorine and other toxic chemicals are potential terrorist targets.” These chemicals are even more vulnerable while in transit, as the Wall Street Journal proved by following graffiti artists as they “tagged” chlorine tank cars within site of the US Capitol building, long after 9-11.
The chemical industry’s own estimates reveal that if the chlorine from just one tank car were released by accident, sabotage or direct attack, the toxic gas could travel two miles in 10 minutes and remain lethal as far away as 20 miles.
Based on testimony by Dr. Jay Boris, Chief Scientist at the US Naval Research Laboratory, 3 minutes after a catastrophic rupture of a rail car in Washington, DC, a lethal cloud could reach the National Mall. On July 4th, when thousands gather to watch the fireworks display, people could die at the rate of 100 per second.
For this reason, Washington DC’s water treatment plant phased-out chlorine gas after 9-11. In New Jersey, after the passage of the Toxic Catastrophe Prevention law, the number of water works using chlorine has dropped from 575 in 1988 to just 22 in 2001.
These precautions are laudable, and verify chlorine reduction as a legitimate chemical security strategy. But ten times more chlorine is destined for PVC plastic than for municipal water treatment. PVC plastic can contain up to 50% chlorine by weight. By comparison, household bleach is typically less than three percent chlorine.[1]
Building materials account for more than 70% of all products manufactured of PVC. If we are willing to change the way we sanitize our drinking water in order to chip away at 5% of the vulnerable chlorine stockpile, what is the overriding interest that justifies keeping nearly ten times that amount on tap to make faux clapboard siding, picket fences, and vinyl flooring?
In an era of security alerts Yellow, Orange and Red, how can PVC be considered green?
In the last 40 years, polyvinyl chloride plastic (PVC) has become a major building material. Global vinyl production now totals over 30 million tons per year, the majority of which is directed to building applications, furnishings, and electronics.
The hazards posed by dioxins, phthalates, metals, vinyl chloride, and ethylene dichloride are largely unique to PVC, which is the only major building material and the only major plastic that contains chlorine or requires plasticizers or stabilizers. PVC building materials therefore represent a significant and unnecessary environmental health risk, and their phase-out in favor of safer alternatives should be a high priority. PVC is the antithesis of a green building material. Efforts to speed adoption of safer, viable substitute building materials can have significant, tangible benefits for human health and the environment. This report describes the full life cycle of PVC in the contemporary building industry from production to disposal.