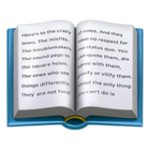
This report explores the association between racially discriminatory housing practices from the 1930s and exposure to oil and gas wells, highlighting the impact of structural racism on environmental exposure disparities in urban areas.
This report evaluates the risk of drinking water contamination in Los Angeles County, California, based on the proximity of supply wells to oil and gas wells, highlighting disparities in risk based on race/ethnicity and measures of structural racism.
The idea of a “plastic building” might bring to mind Barbie DreamHouses or Lego towers, but probably not the real life spaces we occupy every day. However, plastics have a long history of use in construction and are increasingly being used in a wide variety of building products.
What are plastics?
Plastics are synthetic or semi-synthetic materials typically made from fossil fuels and their byproducts.1 Depending on the plastic’s intended use, they may also be combined with a variety of additives such as stabilizers, fillers, reinforcements, plasticizers, colorants, and processing aids, many of which are toxic chemicals that are linked to chronic disease. They are a material of choice in the built environment, however, they come with a host of deeply rooted problems.
Durable plastics are the new “frontier”
As the energy sector shifts away from fossil fuels, the fossil fuel industry has turned toward plastics as a way of maintaining demand for their products.2 An International Energy Report from 2018 showed that petrochemicals, which are used to make plastics, are slated to become the largest driver of global oil demand in the near future.3 Historically, much of the investment has been in single-use plastics, which are increasingly the focus of bans, restrictions, regulations, and product innovation due to their harmful environmental effects.2 To pick up this anticipated slack, petrochemical, fossil fuel, and plastics industries are now pushing to increase their market growth in more durable goods, like building materials.4 The building and construction industry is already the second largest consumer of plastics after packaging.5
Plastics contribute to climate change
Plastics contribute to greenhouse gas emissions at every stage of their lifecycle. Greenhouse gases are released during fossil fuel extraction, transport, feedstock refining, and plastic manufacture, and carbon is released into the atmosphere through degradation and incineration at plastic products’ end of life.6 A 2019 Center for International Environmental Law report concluded that these lifecycle emissions may make it impossible to keep global warming below 1.5 degrees if growth continues as projected.6 Any comprehensive climate change plan must curb the production of plastics.
Plastic is ubiquitous in buildings
Maybe you know that vinyl flooring is plastic, but did you know that latex paint is mostly plastic? That many insulation products are plastic? How about carpet? Plastic-containing products can be found in almost every part of a building, from the waterproofing on foundations to roofing materials. See below for an infographic showing just some of the plastic materials in an average home. The products included are not exhaustive, but rather a list of example product types from Habitable’s InformedTM product categories where a main component is plastic. There are many more products that are predominantly made of plastic, and even more that contain smaller amounts of plastic additives or plastic binders.
Our plastic buildings are driving the growth in fossil fuels at the same time as we are diligently working to incorporate clean energy solutions and decarbonize these very same places.
Hidden costs of cheap plastic
Plastic products are often favored due to their “low cost.” This low retail cost is achieved by avoiding and externalizing the costs of fossil fuels and industrial pollution – and their related chronic diseases – throughout the plastics supply chain. These externalized costs are real and paid for by the BIPOC and low-income communities across the nation who are disproportionately burdened with toxic pollution flowing from refineries, chemical manufacturing, and plastics plants. It is fair to say that most of the stories about environmental justice that you have heard can be linked to plastics manufacturing.
With the building and construction industries anticipating growth over the next several years,7 commensurate growth is to be expected in their use of plastics. Indeed, market trends and projections show a steady increase in polyvinyl chloride (aka vinyl), polystyrene, polyethylene, polyurethanes, and other plastics used in building materials.8
It is, of course, unrealistic to avoid all plastic in building materials at this time, but there are steps we can take to reduce plastic waste, decrease toxic chemical use, and curb the demand for fossil fuels.
Select Better: Avoid worst-in-class plastics where possible.
Prioritize Transparency: Prefer products that provide transparency
Aim for Circularity: Select products designed for recycling.
With all of these plastic products, our buildings may seem increasingly like Barbie’s DreamHouse and a climate nightmare, but as specifiers, designers, architects, contractors, and owners we can do much to control what products end up in our projects. Starting with the recommendations above, we have the power to influence demand for better and safer materials. In the case of plastics, choosing better materials can lead to less reliance on fossil fuels, fewer greenhouse gas emissions, a decrease in toxic chemical use, and a win for our changing climate.
This video describes why plastic ends up in the environment and the solutions needed to disrupt the unsustainable use of plastic by holding manufacturers accountable for the products they make.
Dr. Jonathan Foley, Executive Director of Project Drawdown, talks about how carbon offsets and “net zero emissions” claims are a dangerous distraction to meaningful climate change initiatives.
This report discusses how President Biden’s Executive Orders need to go further than examining energy sources to combat the climate crisis, emphasizing the need for the chemical industry to adapt and innovate, considering its significant impact on greenhouse gas emissions and environmental health.
The Future of Petrochemicals report explores the role of the petrochemical sector in the global energy system and its increasing significance for energy security and the environment, highlighting the need for attention from policymakers.
Not all recycled content materials are created equal – especially when it comes to recycled plastics.
In a report released by StopWaste and the Healthy Building Network, we take an in-depth look at the health implications, supply chain considerations, and potential to scale up recycling of the world’s most common plastic: polyethylene (aka PE). [1] This report, Post-Consumer Polyethylene in Building Products, is the latest installment in our Optimizing Recycling series.
Polyethylene is a material widely used in product packaging, beverage containers, and myriad consumer products. High Density Polyethylene (HDPE), Low Density Polyethylene (LDPE), and Linear Low Density Polyethylene (LLDPE) are all readily recyclable in California. Polyethylene plastic scrap bottles and plastic bags usually have minimal contents of concern and are easily processed into feedstock for new products, including building materials. Despite the great potential for recovery of PE, sizeable barriers stand in the way of a lot more recycling.
The explosive growth in virgin ethylene production on the U.S. Gulf Coast, driven by cheap energy, has meant that most post-consumer scrap PE is either landfilled, incinerated, or sent overseas for processing. [2]
Industry trends in recycling collection technology are also undermining the value of post-consumer polyethylene feedstocks. Pipe and plastic lumber manufacturers in the U.S. require supplies that have minimal amounts of contaminants such as volatile residual substances in packaging and other types of plastics. Yet proportionally less “good material” is coming out of the plastic waste recycling stream due to the rising use of municipal single stream recycling over the past decade. Mixed and low quality scrap materials that come from single-stream recycling centers are more likely to be exported than sorted and screened for high-quality polyethylene scrap. As a result, more recovered plastic bags are exported than processed domestically. [3]
Additives used for plastics can turn into contaminants when recycled. As seen with other recycled content materials, feedstocks with less contamination have an increased potential for recyclability as well as increased value to purchasers. [4] For PE, contaminants come in the form of residual materials from packaging (residue from bottles that contained pesticides, for example), or from additives used in manufacturing to achieve certain product characteristics. Perhaps the most problematic additive to PE products are so-called biodegradation additives used in plastic packaging. These additives (but not the rest of the plastic) degrade when exposed to sunlight or other environmental conditions. When these products are collected and used as post-consumer recycled feedstocks in products like pipes and decking, however, these additives can lower the reliability and value of a manufacturer’s product. This is why, in our report, we recommend that plastic manufacturers stop using degradability additives in all new polyethylene.