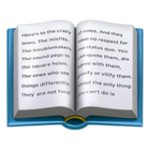
Watch ChemSec’s skit about the SIN List, to learn why hazardous chemicals should be removed from products due to the health and environmental risks they present.
ChemSec’s Marketplace connects products like this car seat with safer alternatives to hazardous chemicals, offering a platform for them to find better matches and reduce their environmental impact.
Phase 2 of this report is the first of its kind plant-by-plant accounting of the production, use, and releases of chlorine and related pollution around the world. It is intended to inform the efforts of building product manufacturers to reduce pollution in their supply chains.
Chlorine is a key feedstock for a wide range of chemicals and consumer products, and the major ingredient of polyvinyl chloride (PVC) plastic. The report includes details aboutthe production technologies used and markets served by 146 chlor-alkali plants (60 in Asia) and which of these plants supply chlorine to 113 PVC plants (52 in Asia). The report answers fundamental questions like:
Key findings include:
Supplemental Documents:
The Global Chemicals Outlook II assesses global trends and progress in managing chemicals and waste to achieve sustainable development goals, with a focus on innovative solutions and policy recommendations.
Discover how bisphenols and phthalates, commonly used in plastics for added strength or flexibility, can disrupt hormone function, and learn ways to reduce their use for improved health in this informative video.
Phase 1 of this report is the first of its kind plant-by-plant accounting of the production, use, and releases of chlorine and related pollution around the world. It is intended to inform the efforts of building product manufacturers to reduce pollution in their supply chains.
Chlorine is a key feedstock for a wide range of chemicals and consumer products, and the major ingredient of polyvinyl chloride (PVC) plastic. The report includes details about the largest 86 chlor-alkali facilities and reveals their connections to 56 PVC resin plants in the Americas, Africa and Europe. (The second phase of this project will inventory the industry in Asia.) A substantial number of these facilities, which are identified in the report, continue to use outmoded and highly polluting mercury or asbestos.
Demand from manufacturers of building and construction products now drives the production of chlorine, the key ingredient of PVC used in pipes, siding, roofing membranes, wall covering, flooring, and carpeting. It is also an essential feedstock for epoxies used in adhesives and flooring topcoats, and for polyurethane used in insulation and flooring.
Key findings include:
Supplemental Documents:
The Future of Petrochemicals report explores the role of the petrochemical sector in the global energy system and its increasing significance for energy security and the environment, highlighting the need for attention from policymakers.
Healthy Building Network’s report on post-consumer carpet feedstocks calls for eliminating over 40 highly toxic chemicals in carpets that threaten public health and impede recycling. These toxics are known to cause respiratory disease, heart attacks, cancer, and asthma, and impair children’s developmental health.
The report outlines strategies to protect public health and the environment by improving product transparency, eliminating dangerous chemicals from carpets, and increasing carpet recycling rates. It also reveals surprising efforts in the industry to remove many of these toxic substances from carpet design.
Building products incorporating antimicrobial additives are becoming increasingly prevalent. Paints, and other touchable surfaces such as countertops, and virtually any product considered as an interior finish may contain one or a combination of antimicrobials. These agents are considered pesticides, but their identity—and related hazards—can be difficult for the average person to discover. This lack of transparency creates a hurdle for the informed selection of products with reduced negative impacts.
No evidence yet exists to demonstrate that products intended for use in interior spaces that incorporate antimicrobial additives actually result in healthier populations. Further, antimicrobials may have negative impacts on both people and the environment. This paper, prepared by Perkins&Will in partnership with HBN, aims to present current information about reported or potential health and environmental impacts of antimicrobial substances as commonly used within the building industry, and to assist architects, designers, building owners, tenants, and contractors in understanding those impacts.
In response to growing concerns over COVID-19, Healthy Building Network (HBN) and global architecture and design firm Perkins and Will reexamined and reaffirmed the conclusions and recommendations of this white paper.
Asphalt (also known as asphalt concrete, bitumen, or road tar) is the most common paving material by far, accounting for a 92 percent share of the 2.5 million miles of roads and highways in the United States. Reclaiming and reusing asphalt has many benefits, including waste prevention, reduction of greenhouse gas emissions, and lower lifecycle impacts compared to virgin asphalt material use.
Keys to increasing the recycling of asphalt and its attendant environmental benefits include simplifying the designs of asphalt mixes, reducing toxic additives in production, tracking materials from production through use and recycling, testing incoming materials for contaminants, and avoiding the addition of cutback solvents and other toxic rejuvenating agents.